

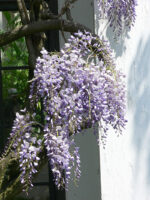





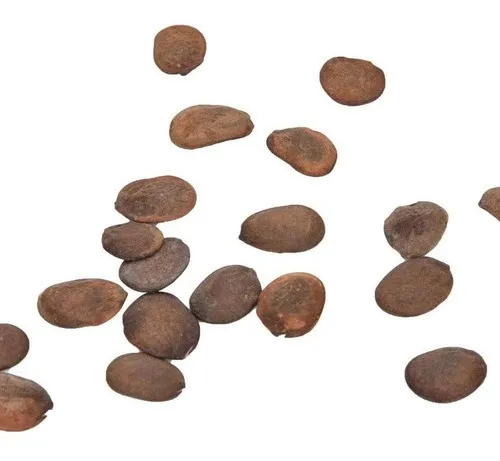



Luojuny Semillas De árboles De Glicina, 100 Unids/bolsa Semillas De árboles De Glicina Decorativas Vibrantes Color Mezclado Semillas De Plantas De Crecimiento Rápido Para Balcón Semillas De Gli
Envío exprés con DHL GoGreen , si realizas el pedido en las próximas 24 horas
- Entrega en 1-2 días laborables
- Envío gratuito a partir de 49,90 €
- 62 días de devolución gratuita
Ficha del producto
🍃[Buena elección] - Como es fácil de germinar y fácil de cuidar, puede obtener fácilmente plantas verdes vibrantes y plantas trepadoras bonsái decorativas. lleno de flores adornan tu jardín. 🍃[Escenas adecuadas]: es adecuado para patios traseros, balcones, jardines, patios, macizos de flores, granjas, patios, etc. 🍃[Fácil de plantar]: estas semillas no requieren ningún cuidado o mantenimiento especial, ya que son fáciles de cuidar y cultivar debido a su resistencia a la sequía, rápido crecimiento, resistencia a la intemperie y alta germinación. tasa. Para los entusiastas de la horticultura que aman plantar plantas, estas semillas desempeñarán plenamente su papel. Hecho de material de semilla natural, este producto es seguro, respetuoso con el medio ambiente y saludable. Permita una ligera diferencia de dimensión debido a diferentes medidas manuales. Nombre del artículo: semillas de glicinaMaterial: semillasCaracterísticas: crecimiento rápido, flor morada, plantas trepadoras. Este producto no solo puede convertirse en la decoración de su jardín, sino que también puede convertirse en sus platos novedosos con sus características comestibles. Rosal Banksiae Luojuny Semillas De árboles De Glicina, 100 Unids/bolsa Semillas De árboles De Glicina Decorativas Vibrantes Color Mezclado Semillas De Plantas De Crecimiento Rápido Para Balcón Semillas De Gli Semillas Flor De Loto Es adecuado para plantar en patios, patios, balcones, patios, jardines, oficinas y parques. El paquete incluye:1 bolsa de semillas de glicinia (50 piezas)& lt;/p & gt;& lt;/p & gt; 🍃[ Cantidad ] - Cada bolsa tiene alrededor de 50 piezas de semillas. 🍃[ Adaptabilidad ]: se puede adaptar a la mayoría de los suelos, pero en suelos profundos que drenan libremente, con suficiente luz solar y agua estable, la humedad, la temperatura y el oxígeno adecuados pueden producir las mejores plantas. Cantidad ] - Cada bolsa tiene alrededor de 50 piezas de semillas. [Escenas adecuadas]: es adecuado para patios traseros, balcones, jardines, patios... )Notas:La cantidad es de aproximadamente 50 piezas, debido al cálculo manual, la cantidad podría tener 1-5pcs más o menos, espero que pueda entender, gracias.
Opiniones de los usuarios (621)
Sobre el proceso de verificación
No se ha comprobado si estas opiniones sobre productos proceden de consumidores que hayan utilizado o adquirido realmente dicho producto a menos que dicha valoración esté marcada como "opinión verificada".
Más información sobre el proceso de verificación
Media de 621 valoraciones
Menos CO2. Más responsabilidad.
- Climáticamente neutros
- Comprometidos con el clima